The culture of occupational safety
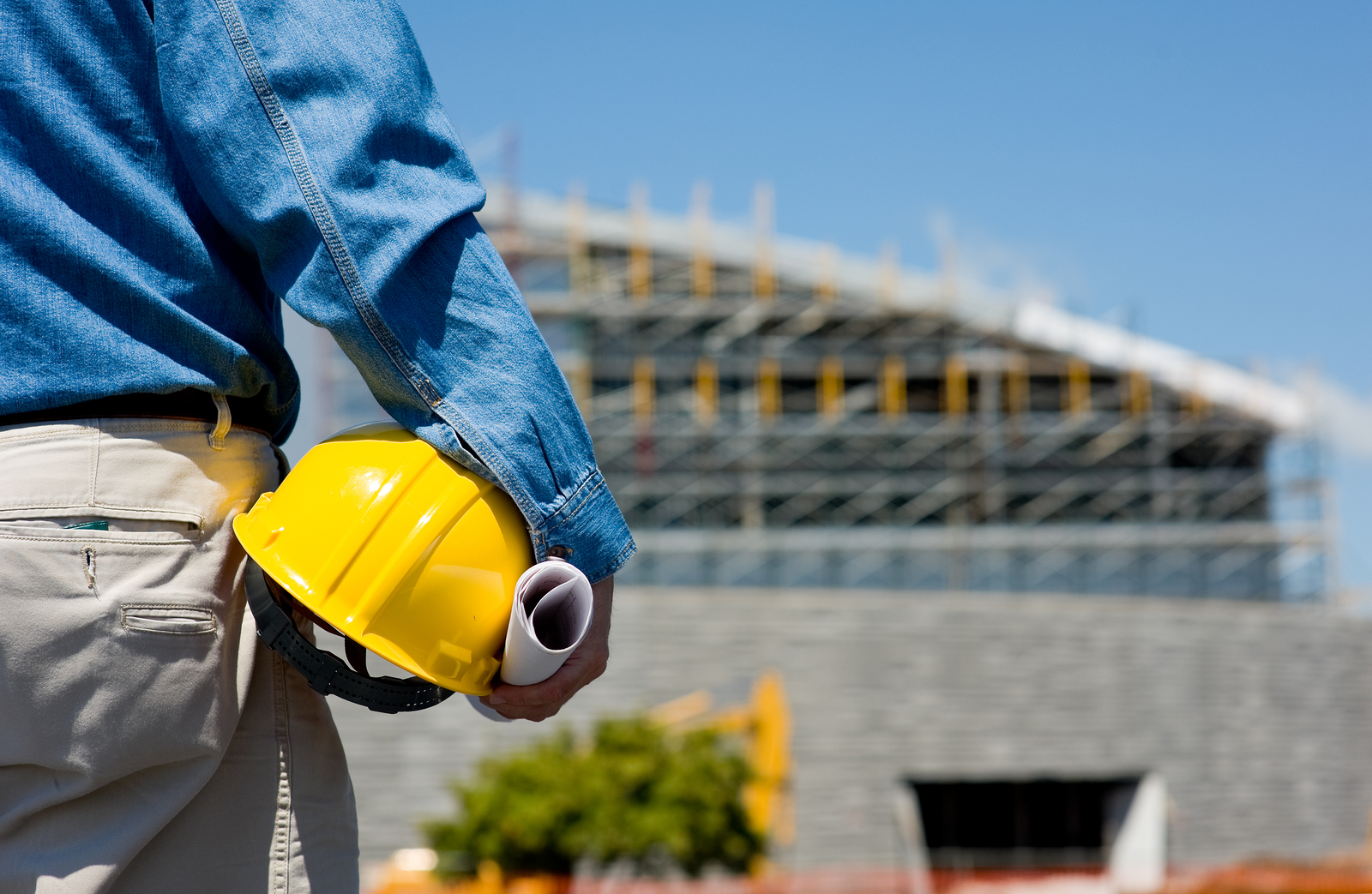
On April 26, 1986, the worst nuclear industry accident in human history has occurred in the Soviet Socialist Republic of Ukraine. Following the Chernobyl incident, the International Nuclear Safety Group has introduced the term “occupational safety” for the first time. However, the Health and Safety Committee of Great Britain stated that “An organization’s health and safety systems are reflections of an individual’s or group’s value, attitudes, concepts, behaviors and qualifications.” The organization went further to say” This has helped the culture of safety be developed and understood by the public. An organization with a positive culture of safety is one that has a trust based relationship, an understanding of the significance of security and effective preventive measures.”
In Mongolia’s case, occupational safety has been prioritized as a key concept starting the socialist society but has not become a part of companies’ cultures up until ten years ago. In the old system, the head of the organization was only responsible for constructing the plan while the labor safety engineer always had requirements set for the staff and supervised the workers like a parent. The flaw in it was that the workers would not particularly care about their own safeties and in case of an accident, the labor safety engineer was always blamed. A study carried out on industrial accidents theorizes that 98 percent of accidents created by system errors. By constantly improving an organization’s leadership system, the culture of safety can be created.
The occupational health and safety system introduced OHSAS1800:2007 has been updated to become ISO45001:2018 by the International Organization for Standardization. As for its implementation, it has widely infiltrated the mining sector which is one with the most risks and accidents. In particular, large mines that have had stable and lengthy operations such as the Oyu Tolgoi, Erdenet, Baganuur, Shivee-Ovoo, and Boroo Gold are more focused on occupational safety. For instance, Oyu Tolgoi is considered to be a role model in this matter, but the company is a mega project and an international company with many investors. By no means can we compare it to our domestic smaller companies that get their investment by the month. Even so, implementing occupational safety to the organization is a greater investment which protects from accidents and it is more so dependent on the mentalities of the leaders as opposed to financial restrictions. Therefore, the budget of one billion MNT is allocated out of the Occupational Safety and Health in Social Insurance find to give training to companies. However, this training does not reach the target group which is the company heads and instead is conducted as a half baked training mentioned Deputy Director of the DAT Consulting LLC N.Algaa in an interview with our magazine.
Article 27.1 of the Law on Occupational Safety and Health (OHS) passed in 2008 stipulates “The responsibility of ensuring labor safety, improvement of labor conditions and the implementation and enforcement of laws and regulations shall be borne by the directors/ owners of the business entity and the employer directly.” The employer must establish and OHS structure and staff on board. Furthermore, Article 26.2 states that the budgetary entity shall cover at least 0.5 percent and depending on the risk level of the business entities and organizations, at least 1.5 percent of the cost of production and services must be allocated to ensure OHS, preventing industrial accidents, acute poisoning and occupational diseases.
However, even when the legal and regulatory framework is provided, a large number of industrial accidents and injuries still occur frequently in Mongolia. Looking at the statistics of the past three years, industrial accidents and acute poisoning have been reported 332 times in 2016 and 2017, while such cases occurred 283 times in 2018. If it is analyzed by the sectors, then accidents and injuries are high in the mining, defense, transportation and construction sectors. There are approximately 40 thousand people working in the Mongolian economy pillar sector of mining. In the sector, there were 61 accidents reported in 2016, 55 in 2017 and 73 in 2018.
The last accident took place in February 28, 2019 in Zaamar soum of Tuv Province, where a wall collapse in the mine of Eco Altan Zaamar LLC lead to the death of four. Additionally, on April 17, 2019, there was a loss of methane gas in the Central Sewage Facility and four people sank into the sludge and died while eight were hospitalized. Over the last three years, 88 people lose their lives due to industrial accidents and acute poisoning. Unfortunately, for the case of Mongolia, the value of lives and and the amount of compensation is truly pitiful, and thus, we are at a loss of words to describe its condition. Nonetheless, since we can’t be silent about the issue, the word “terrifying” is perhaps more suitable. Article 97.1.3 of the Labor Code states that compensation for the death of an employee due to industrial accidents, acute poisoning and occupational diseases shall be paid more than or equal to the employee’s salary of 36 months. The National Statistic office announced that the average salary of Mongolians stand at 1.1 million MNT in February 2019. In other words, this means that the life of a Mongolian person is valued at 36.6 million MNT. Regardless of the amount of compensation, there is nothing in this world that could replace the life of a human being. For this reason, the most precious thing to come out of a mine are the miners themselves. There is no guarantee that there will not be accidents in the mining sector. Though there are numerous conditions in the workplace that could result to accidents, one of the main reasons for accidents in mining is because of the phrase “The law lasts three days in Mongolia”. Even though the management system and legal environments were put into place, this is not being implemented at all. The law enforcement agencies issue a resolution and decree, but they do not work.
On the other hand, the understanding of OHS does not exist in the minds of Mongolians at all. The management of businesses need to understand that through following OHS, there are numerous benefits to the company. Their costs are lowered, the workers become more active, the environment becomes stable, it is advantageous for them during tender selections, for the goods and services produced, and it becomes a reason for people to consume their products. “The employer’s one euro spent on occupational safety measures return twice as much as benefits.” highlighted the occupational safety and health survey of the European Union. Seeing the culture of occupational safety in a broader sense, it is really all about how each person acknowledge and pay attention to their own safety. For example in disaster prone areas like Japan, people are taught how they can bring themselves and others to safety during earthquakes from an early age. Similarly experts highlight that that starting from kindergarten, the knowledge of preventing yourself from any risks, living in a safe and healthy environment, and creating a sense of responsibility for everyone to build a culture of safety should be taught throughout all levels of education.
In today’s society, the labor and safety culture has not yet been understood and this article aims to provide the public with the clear perception. Ultimately let’s emphasize that everyone has the right to live and work in a healthy and safe environment. Only then can this culture grow more.